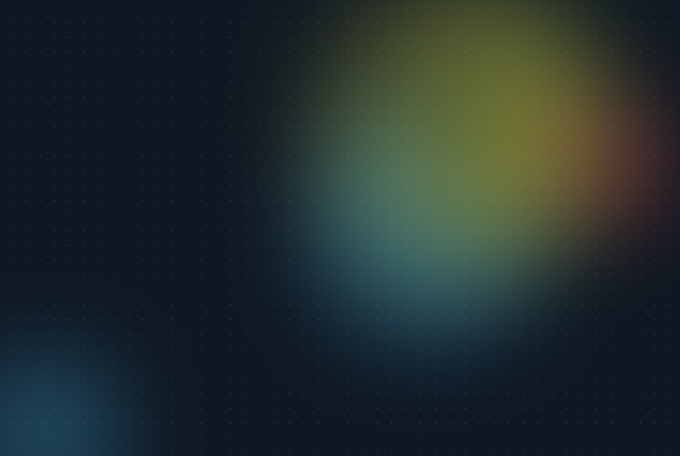
Laser Marking on Stainless steel
What Do i get here?
A full insight with useful information about laser marking on stainless steel: The advantages of laser marking on stainless steel compared to other industrial marking processes. Various laser marking methods, their specific advantages and the associated challenges. Useful and practical tips from our laser lab. Overview of popular industries in which laser marking is heavily used and a summary of the most commonly used laser types for stainless steel marking with their specific strengths and applications.
Advantages of Laser Marking on Stainless Steel Compared to Other Methods
Laser marking on stainless steel has proven indispensable in numerous industries. It surpasses conventional methods such as etching, mechanical engraving, or ink marking in several ways.
Unlike some traditional methods, laser marking is particularly gentle on materials. Due to the precise application of laser power and the non-contact marking process, the material is minimally affected. This can reduce material loss due to damage during the marking process. Furthermore, laser marking generates no waste, and the use of chemicals such as solvents or acids is unnecessary.
The reduction of material damage during the marking process, low maintenance effort as well as the absence of consumables and mechanical wear parts makes laser marking on stainless steel a particularly cost-effective marking method with special relevance for the industry.
Laser marking on stainless steel offers higher speed and efficiency compared to many traditional methods. The focused laser beam works precisely and can apply various markings at high speeds. Traditional methods, such as engraving or etching, often require time-consuming setup and manual interventions, which can lead to longer processing times. Ink marking requires drying times, increasing the overall processing time.
Laser marking on stainless steel offers a wide range of design possibilities. It can create not only text but also logos, barcodes, and complex graphics with high detail accuracy. This versatility is particularly relevant for businesses looking to highly customize their products flexibly. In contrast, traditional methods are typically limited and do not offer the same freedom in design and highly flexible text, graphic and marking size customization.
An outstanding advantage of laser marking on stainless steel is its exceptional precision and detail accuracy. Focused laser beams make it possible to create fine lines, letters and symbols on a large scale or even in tiny font sizes and microscopic dimensions of just a few µm. In comparison, conventional methods like mechanical engraving or etching often produce coarser markings that are less precise. Ink marking can smudge or fade, leading to blurriness and reduced detail accuracy.
Stainless steel is exposed to extreme environmental conditions in many applications, whether in food processing, medical technology, or aerospace. Depending on the method used, laser marking is known for its high resistance to abrasion, corrosion, and chemicals. Markings remain durable and easily legible even under adverse conditions.
Are you looking for suitable laser sources, scan heads or optics for your new laser marking system and your process development? Or maybe for further information, such as specific technical data, delivery times or prices?
Please let us know:
Laser Annealing Marking on stainless steel
Annealing marking or color marking on stainless steel is a method in which the focussed laser beam heats the material's surface, creating a high-contrast and durable marking.
By locally generating temperatures between 200 and 700 °C, different annealing colors can be achieved. In addition to color marking, the typical goal of laser annealing is to create a "perfectly black" marking.
Annealing marking on stainless steel offers the following advantages:
Gentle on the material surface:
Annealing marking is particularly gentle on the material surface, as no material is removed and therefore damage is prevented.
Strong contrast:
The markings created by annealing are characterized by a strong contrast to the material surface. Perfectly black markings are possible.
Color marking possible:
Annealing marking allows for marking stainless steel in various colors, depending on the material and parameter settings. It provides flexibility and design options in product labeling.
Versatile design options:
Laser annealing marking can be used to create fine lines, detailed fonts, logos and graphics with precision, opening up a wide range of design possibilities.
Potential Challenges of annealing marking
Slower compared to alternative laser marking methods. Especially when the desired color can only be achieved through multiple processing steps and repeated heat input.
Less precision in the case of micro-markings, as a larger laser focal spot is often required to achieve the desired color and contrast effect.
Especially in environments with aggressive chemical influences or on low quality steel.
The color range is limited and certain shades may not be achievable or may require extensive tuning of the laser parameters.
Annealing marking typically generates heat within the material, which can lead to undesirable heat propagation in some applications.
A tip from our laser lab on annealing
To do annealing marking on stainless steel, the material must be heated in a controlled manner without melting or vaporizing it. In many cases, this requires a reduction in the power density on the material.
An efficient way to implement this technique is to work out of the focal plane of the laser, thereby increasing the laser spot size. This distributes the same laser power over a larger area and reduces the energy density.
But it should be noted that this method is not the best choice for consistently high-quality marking results in mass production.
Alternatively, system components can be selected that generate a larger spot size with optimum power density in the focus of the laser beam. In particular, the suitable selection of the beam expansion or beam reduction and the F-Theta lenses plays an important role, as they have a significant influence on the focus size and power density.
Laser Engraving on Stainless Steel
Laser engraving on stainless steel is a marking method in which the finely focused laser beam removes material through vaporization to create precise and highly durable markings.
Laser engraving on stainless steel offers the following advantages.
Great visibility:
Engraving removes material, resulting in deep and long-lasting markings, ensuring great readability and visibility.
Resistance to external factors:
Engraved markings are highly resistant to abrasion, corrosion, and chemicals, ensuring the long-term legibility of markings, even under demanding environmental conditions.
Outstanding precision:
Engraving provides exceptional precision and control over marking depth and intensity, which is particularly important in industries with strict quality requirements.
Design versatility:
Laser engraving allows for the creation of fine lines, detailed fonts, logos, and graphics, offering a wide range of design possibilities.
Reduced heat input:
In comparison to annealing marking, which is based on heating the material, engraving directly vaporizes the material so that the surrounding material is heated less. This reduces the risk of material deformation.
Potential Challenges of Laser Engraving
Since material removal occurs layer by layer, deeper or extensive engravings may take more time than methods that create only surface markings.
To cause vaporization and achieve high-quality engravings, a sufficiently high-power density on the material is necessary, which requires fine laser focusing.
Depending on the engraving requirements, increased laser power is typically needed to speed up the process time.
Additionally, changes in material properties and surface roughness caused by laser engraving should be considered.
More aggressive parameters are used for efficient ablation. Depending on the depth of the marking and quality requirements, it may be necessary to run cleaning passes with gentler parameters in between so that the laser focus for ablation is not scattered by the increasingly rough surface of the engraving bed.
A tip from our laser lab on Engraving
If engraving needs to be deep, extensive, or particularly fast, it is highly advisable to use a pulsed laser with medium to high output power. High pulse energies and pulse peak powers are very helpful when vaporizing stainless steel. Low pulse peak powers cause heat input and tend to lead to material melting without vaporization.
A particularly fine laser focus with high power density is helpful and can be achieved by widening the laser beam as much as possible before focusing. It is important that the beam expander, laser scan head and focusing lens are perfectly matched to each other. Short focal lengths also support a fine laser focus with high power density.
For particularly deep engraving processes, it is advisable to develop different parameter sets for material removal and surface smoothing. Depending on the engraving depth, the use of a 3-axis laser scan head may be necessary to adjust the focus plane according to material removal, ensuring it remains precisely on the surface of the engraving.
For deeper engravings, the used F-Theta lens should always be telecentric to avoid shading due to the processing depth and angles of incidence. As a reference, you can take a look at our telecentric lenses for 1030 - 1080 nm or 355 nm.
Laser Ablation on Coated Stainless Steel
Ablation marking on stainless steel is a process where coating material on the stainless steel is removed by vaporization to create a high-contrast, precise and permanent mark.
Ablation marking on stainless steel offers the following advantages.
High process speed:
Selective ablation of thin coatings allows high process speeds. Compared to conventional laser engraving, the underlying material is not removed.
High-contrast and durability:
Depending on the color of the coating, ablation marking produces highly legible markings. Resistant to abrasion, corrosion, and chemicals, ensuring readability even in challenging environmental conditions.
Versatility and Adaptability:
The process allows the precise creation of various markings on coated stainless steel, including fine lines, fonts, logos, graphics, and more.
Low Heat Input:
Ablation marking generates less heat in the material compared to conventional annealing marking, which reduces the risk of unintentional material deformation.
Potential Challenges of Laser Ablation marking
Finding the right process parameters is an important challenge. The process should be fast, but not too aggressive to avoid damaging the stainless steel under the coating. The choice of suitable laser power, frequency, pulse width, marking speed and other parameters influences the efficiency of the ablation and the quality of the marking.
In order to vaporize the coating and achieve high-quality ablation, a sufficiently high power density is required on the material, which requires fine focusing of the laser.
Removing the coating exposes the underlying material. This can locally change the properties of the workpiece surface.
A tip from our laser lab on Ablation marking
If you find that not only the coating has been removed, but also the underlying material has been engraved, you can either reduce the output power of the laser or increase the frequency and speed of the scan head. By increasing the pulse frequency, the pulse energy is automatically reduced and the individual pulses are less aggressive.
Output power [W] / Pulse frequency [kHz] = Pulse energy [mJ]
e.g.
100 Watt / 100 kHz = 1 mJ
100 Watt / 150 kHz = 0.67 mJ
You may have to increase the scan head speed if you have increased the pulse frequency, as otherwise the pulses may overlap unintentionally.
Polishing Marking on Stainless Steel
Laser polishing marking on stainless steel is a highly precise process in which a finely focused laser beam modulates the material's surface to create an impressively smooth and durable marking.
Laser polishing marking on stainless steel offers the following advantages.
Highly glossy markings:
Laser polishing marking generates highly glossy and reflective markings on the surface of stainless steel. This not only provides aesthetic appeal but also enhances readability and visibility.
Precision and detail:
Laser polishing marking allows for the creation of highly precise and detailed markings, including fine fonts, intricate graphics, and logos. This offers a wide range of design possibilities.
Design versatility:
Laser polishing marking allows for the creation of fine lines, detailed fonts, logos, and graphics, offering a wide range of design possibilities for product marking.
Material-friendly:
Unlike some other marking methods that remove material, the surface of stainless steel remains largely intact during polishing marking. This minimizes the risk of damage.
Potential Challenges of Laser Polishing marking
Laser polishing marking of stainless steel is very effective, but comes with some technical challenges. These include the need to fine-tune the power density of the laser on the surface and the marking parameters to achieve the desired gloss effects.
Achieving consistent and uniform polishing marks can be a challenge, especially on large or unevenly shaped workpieces.
During polishing marking, the surface of the material is precisely and carefully melted and smoothed. This creates local heat in the material.
A tip from our laser lab on Polishing Marking
For clean polish markings on stainless steel, the material must be melted and smoothened in a controlled manner without engraving or annealing it accidentally. In many cases, this requires a reduction of the power density on the material.
For parameter determination, it is very helpful to create a larger laser parameter matrix in the laser software and then laser it on a material sample. This allows a large number of parameter sets to be tested at once and significantly reduces the time and effort required for manual testing of individual parameters.
If a parameter set in the matrix achieves an apparently good result, it should be analyzed under the microscope so that the laser parameters can be adjusted if necessary.
Holographic laser marking on stainless steel
Laser holographic marking on stainless steel represents an advanced method in which a laser beam is used to create holographic markings on the surface.
Laser holographic marking on stainless steel offers the following advantages.
High degree of individuality:
Holographic markings allow for highly individual and visually appealing marking of stainless steel products. Complex holographic patterns, images, and texts can be marked with amazing detail, offering a wide range of design possibilities.
Eye-catching glossy colors:
Holographic markings stand out for their unique optical effects. Depending on the viewing angle and lighting, the color spectrum changes in a fascinating way, which is not only aesthetically pleasing but also offers additional opportunities in terms of counterfeit prevention.
Material-friendly:
Like polishing marking, holographic marking preserves the surface of stainless steel. It does not cause indentations or damage and is gentle on the material.
Potential Challenges of Laser Holographic Marking
Hologram marking on stainless steel is an absolute eye-catcher, but requires structure and patience in finding the parameters. This includes the need to fine-tune the power density of the laser on the surface and the marking parameters in order to achieve the desired hologram effect.
Achieving consistent and uniform holographic markings can be a challenge, especially on large or unevenly shaped workpieces. Holographic marking is very difficult on uneven surfaces.
Holographic laser marking typically generates heat within the material, which can lead to undesirable heat propagation in some applications.
A tip from our laser lab on Holographic Marking
For a holographic effect on stainless steel, the material must be marked without engraving it accidentally. In many cases, this requires a reduction of the power density on the material.
For parameter determination, it is very advantageous to create a comprehensive laser parameter matrix in the laser software and then apply it to a material sample. This procedure enables the simultaneous testing of numerous parameter sets, which significantly reduces the effort required for the manual testing of individual parameters.
industries and applications For Laser Marking on Stainless Steel
Laser marking on stainless steel has established itself as the preferred method for the permanent marking of products and components in various industries. Its versatility, precision, and durability make it an excellent choice for a wide range of requirements.
Automotive and Electric Mobility
The automotive industry is a key sector that widely uses permanent laser marking on stainless steel as a solution. It is of great importance for the traceability of components and compliance with strict quality standards. Whether it is the marking of battery cells, engine components or car body parts, it has become indispensable for efficient and sustainable material marking in the automotive industry
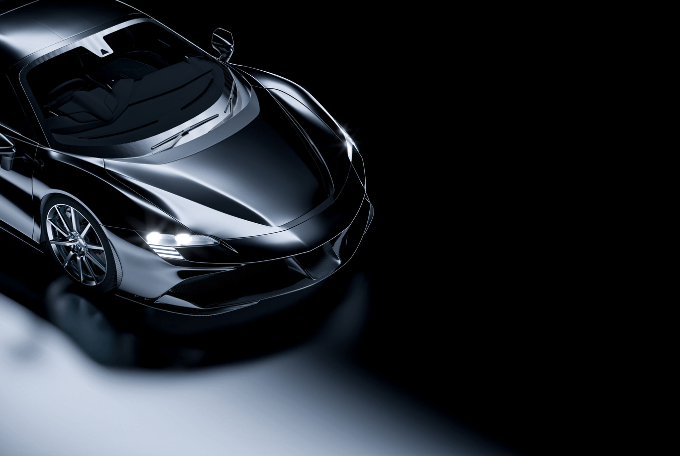
Medical Technology
In the field of medical technology, laser marking on stainless steel plays a central role in the marking of medical devices, instruments and implants. The markings on these products must meet the requirements for medical hygiene. They must be durable and clearly visible throughout the entire product life cycle. Laser marking offers the required precision and durability without compromising the sterility of the medical devices.
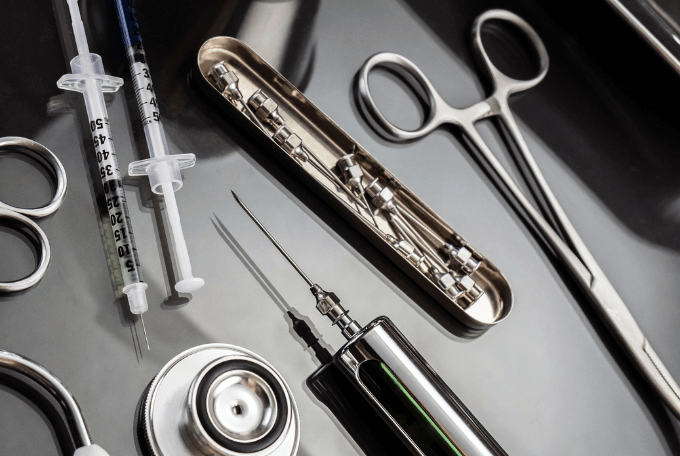
Mechanical Engineering and Tools
In mechanical engineering and the tool industry, laser marking on stainless steel has been widely adopted for several years. Tools, machinery, and components must be marked with permanent identifications to ensure the quality and traceability of products. With laser marking, the finest markings can be applied to tools and machines without damaging the surfaces or visually impairing the product.
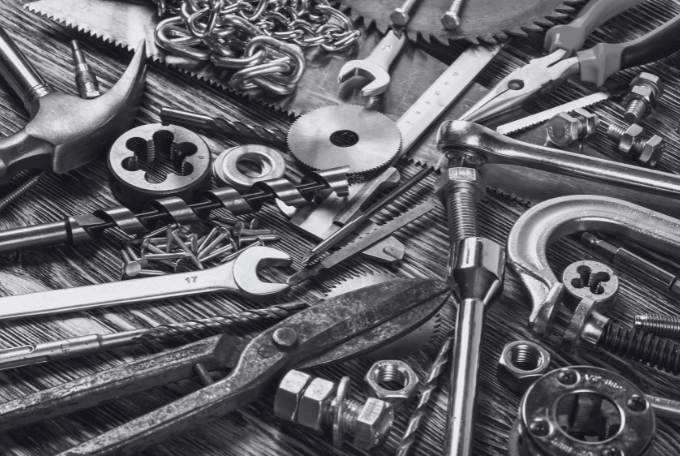
Food industry
In the food industry, hygienic marking of stainless steel containers, equipment, and components is essential. Laser marking is perfect for this purpose as it generates no contaminants and is easy to clean. Laser marking allows for the application of information, warning labels, and logos on stainless steel containers and equipment without negatively affecting the material's positive properties, ensuring hygiene and safety. This is particularly important for compliance with regulatory requirements and quality standards.
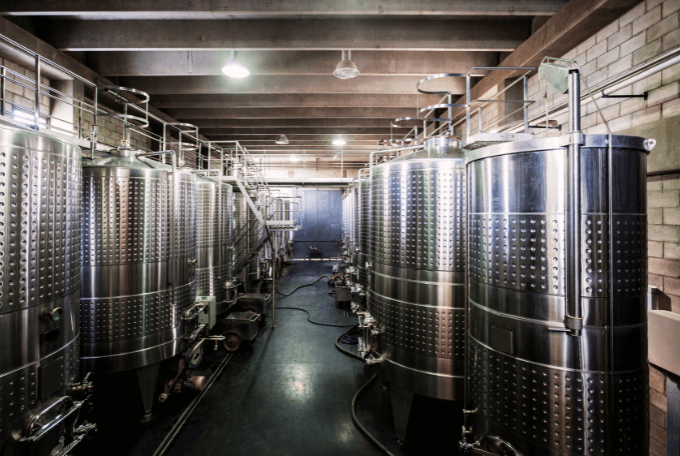
aerospace
The aerospace industry requires precise and durable markings on a variety of stainless steel components and parts. These markings serve the identification, quality control, and traceability of parts in aircraft, rockets, and satellites. Markings must withstand the extreme conditions, do not fade or wear off or negatively affect the positive material properties. The precision and versatility of laser marking are crucial to support safety and reliability in this industry.
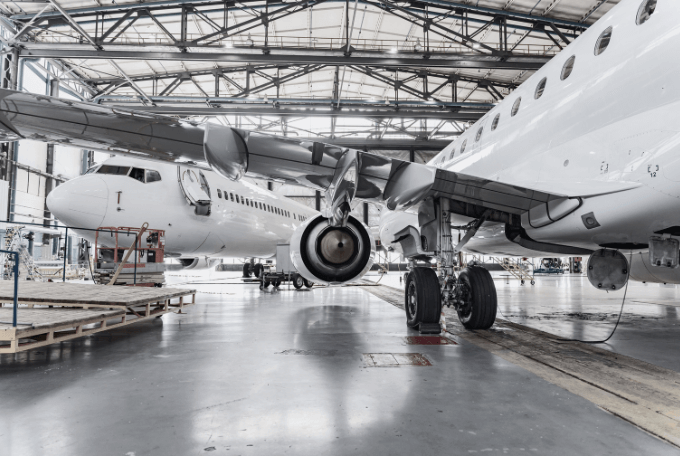
Which Stainless Steel for Laser Marking?
Stainless steel is an extremely popular material due to its durability and versatile applications. Combined with the precision and sustainability of laser marking, it provides an ideal solution for permanent marking on a variety of surfaces. To achieve the best results in laser marking on stainless steel, it is essential to make the right choice of stainless steel, to consider the surface finish, and to prepare the metal as needed.
Which types of Stainless Steel are best suited for Laser Marking?
Steel comes in different alloys, some of which are more suitable for laser marking than others. In general, stainless steel is most commonly used for laser marking due to its excellent durability and corrosion resistance. In particular, austenitic stainless steels of the 300 series (e.g. 304 and 316) and ferritic stainless steels of the 400 series (e.g. 430) are well suited for laser marking. They react well to the effect of the laser beam and produce clear, high-contrast markings.
When laser marking stainless steel, it should be noted that alloy-specific factors can influence the efficiency of the marking. With some types of stainless steel, surface oxidation can occur during the marking process, which can impair the legibility of the marking. To overcome this problem, the use of marking additives or the use of MOPA fiber lasers or picosecond lasers can be considered.
In addition, stainless steel variants with a particularly high carbon content should be avoided, as they can lead to material discoloration and oxidation during marking.
In order to assess the suitability of a particular stainless steel for laser marking, it is advisable to carry out material tests.
Steel Surface finish and preparation
The surface finish of stainless steel plays a crucial role in the quality of the laser marking. A smooth and polished surface is ideal as it allows for uniform and high-contrast marking. Rough or uneven surfaces can result in uneven markings.
To optimize the surface finish, the steel can be cleaned and polished before marking. Sandblasting, grinding, or laser polishing can create a smooth surface that is perfect for laser marking.
Stainless steel is an excellent material for laser marking. Provided the right stainless steel grade is selected, specific material requirements are considered, and the surface is appropriately prepared before marking.
Popular laser types for laser marking on stainless steel
Pulsed MOPA Fiber Lasers, DPSS UV-Lasers and Picosecond Lasers are typically used for laser marking stainless steel. Each of these laser types has its own special strengths and areas of application in the laser marking on stainless steel.
Pulsed MOPA Fiber Lasers
Pulsed nanosecond MOPA fiber lasers have become one of the most commonly used laser types for material marking.
Reasons for this include their versatility, durability, reliability, compact design, low maintenance and exceptional cost efficiency.
They are well known for their adjustable pulse width, high pulse peak powers and pulse energies, high beam quality, particularly fast reaction speed, durability and performance stability as well as their minimal maintenance requirements and the possibility of application and system-specific laser configuration.
MOPA fiber lasers serve as versatile tools for laser marking on stainless steel at the wavelength of 1064 nm.
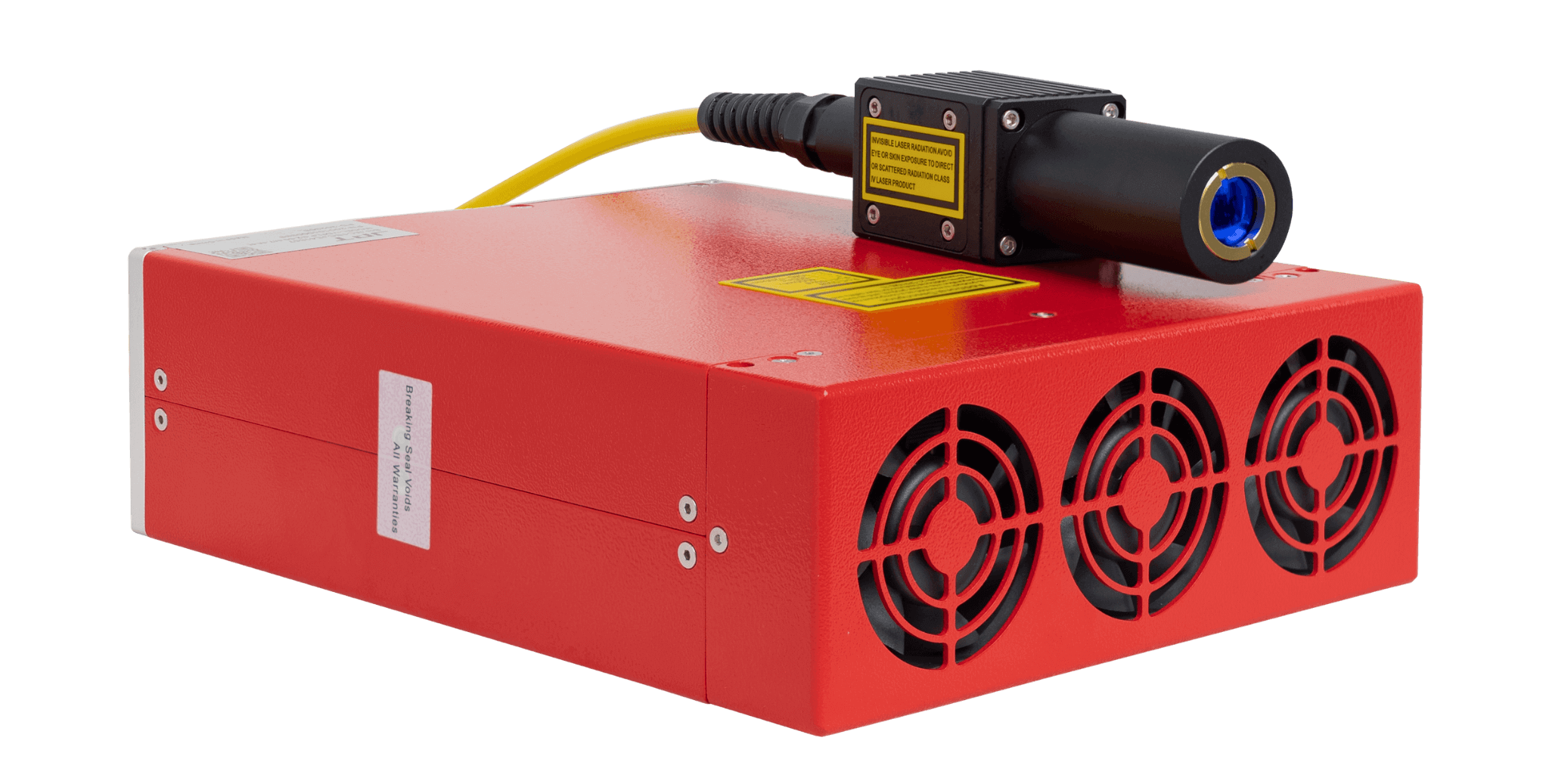
DPSS UV Lasers / nano
DPSS UV Lasers work with an extremely short wavelength of 355 nm, resulting in impressively small focus diameters and therefore outstanding precision in material processing.
They are characterized by very fine focusability combined with high power density and minimal heat input into the material and are therefore ideal for creating particularly precise and microscopically small markings on stainless steel.
Under otherwise identical conditions, a UV laser at 355 nm can be focused about 30 times finer than a CO2 laser with the same output power at 10,600 nm or 3 times finer compared to 1064 nm.
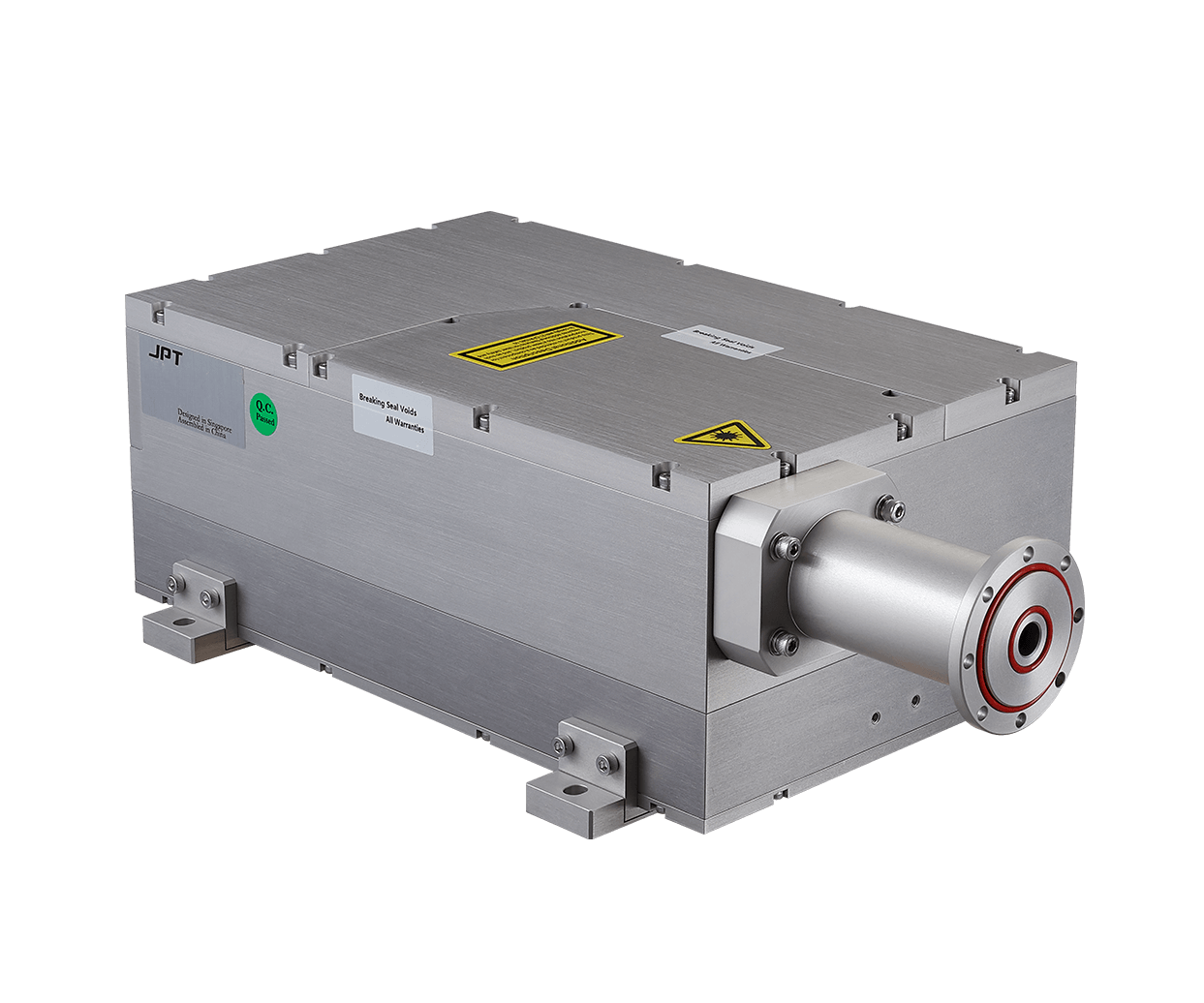
Picosecond Lasers Ultra-short Pulse
Highest precision and minimal heat impact: Picosecond lasers are one of the latest advancements in laser marking technology.
Picosecond lasers work with ultra-short pulses with a duration of just a few picoseconds.
They enable exceptionally high peak pulse powers and minimal heat impact on the material during the marking process: So-called "cold processing".
This makes them the perfect choice for marking thermally sensitive workpieces, as they almost completely eliminate the risk of thermal damage to the material.
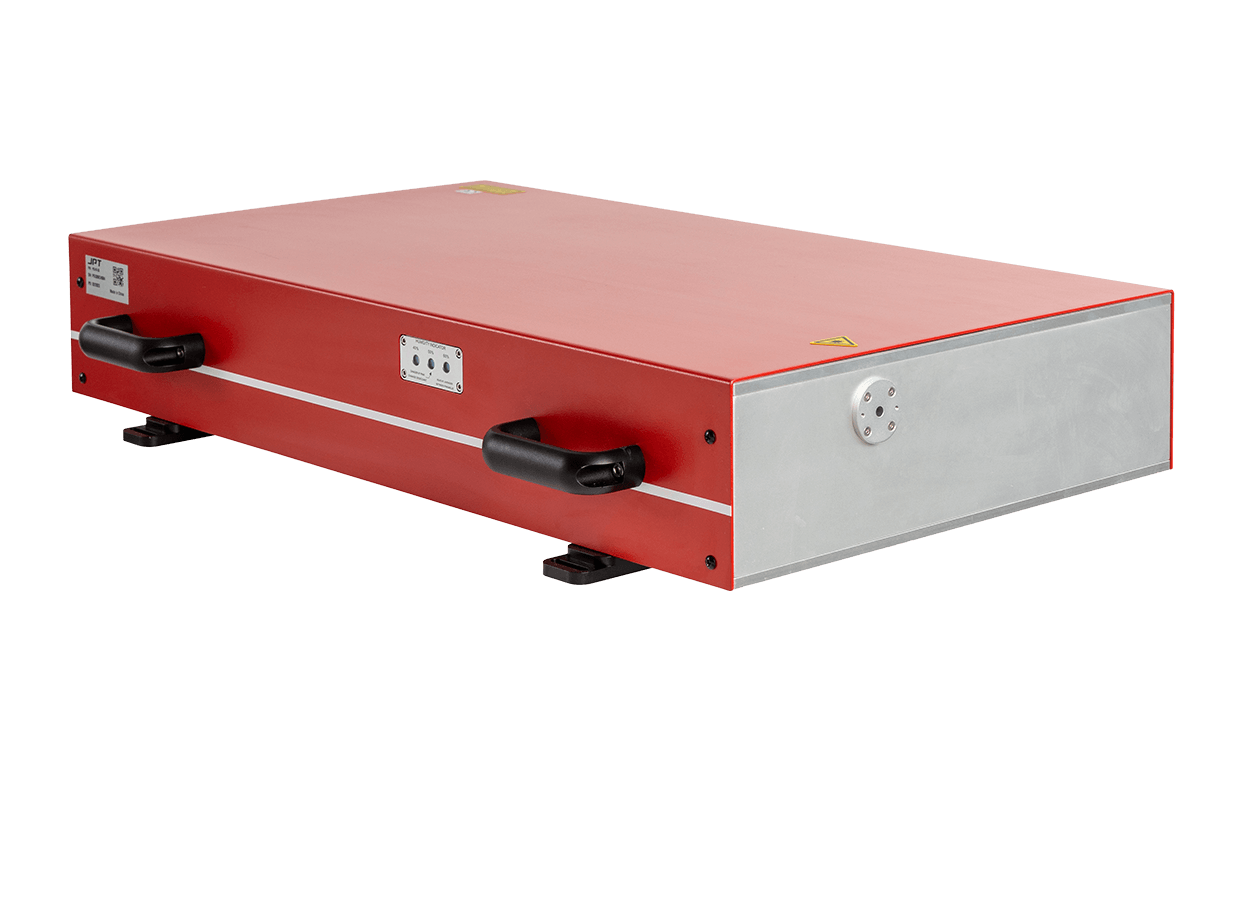