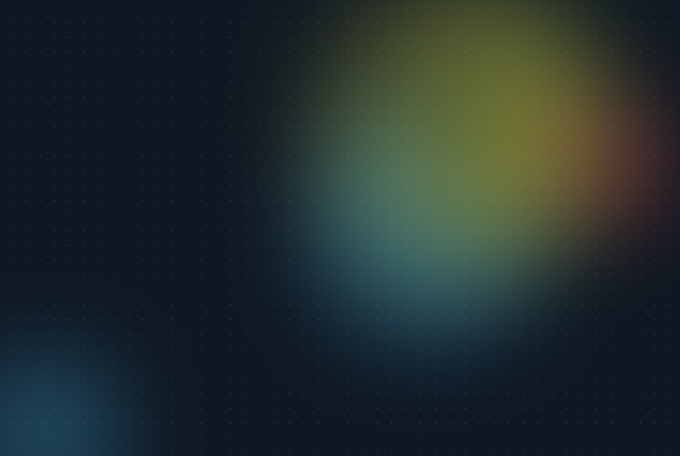
Basics of laser marking
What is Laser Marking?
Laser marking, also known as laser engraving, laser coding, or laser etching, is a process using a focused laser beam to create permanent markings on a variety of materials, ranging from metals to plastics, crystals, or organic substances.
The basic concept of laser marking is to generate a controlled interaction between the focussed laser beam and the material, which results in local heating, melting, or vaporization.
The marking is created by local material removal, controlled color changes or changes to the surface structure. Depending on the material, the laser hardware and finely tuned process parameters.
Laser marking has proven to be essential in all industries where environmentally friendly, precise, cost-effective, fast, permanent, and material-friendly product marking and customization are important.
the Advantages of laser marking
Laser marking allows extremely accurate, permanent and easily recognizable markings on a variety of materials. It helps to ensure complete traceability of products or assemblies throughout their life cycle.
Laser marking is also used to individualize products visually or haptically by applying structures, patterns, text, graphics or microscopic brand protection feature.
The scope of applications for laser marking covers an impressive range of materials and marking methods.
Whether metal, plastic, crystalline or organic material. Laser marking has established itself as a versatile solution. It can be flexibly adapted to the individual requirements of product marking in various industries and markets.
Unlike many other industrial marking processes, laser marking does not require the use of chemicals or consumables.
This helps to reduce the environmental footprint of product marking and supports sustainable production principles.
Thanks to the non-contact and particularly material-friendly and precise marking, waste in the marking process can be reduced or avoided completely.
By eliminating chemicals and consumables, the variable costs of product labeling can be drastically reduced.
Are you looking for additional information on laser sources, scan heads or laser optics for your a new laser marking system or process development?
Or are you interested in other information?
Please let us know.
Structure of a typical laser marking system
Simply click on the hotspot in the image below and find out about the function of the most important laser-specific components in an industrial laser system for marking applications.
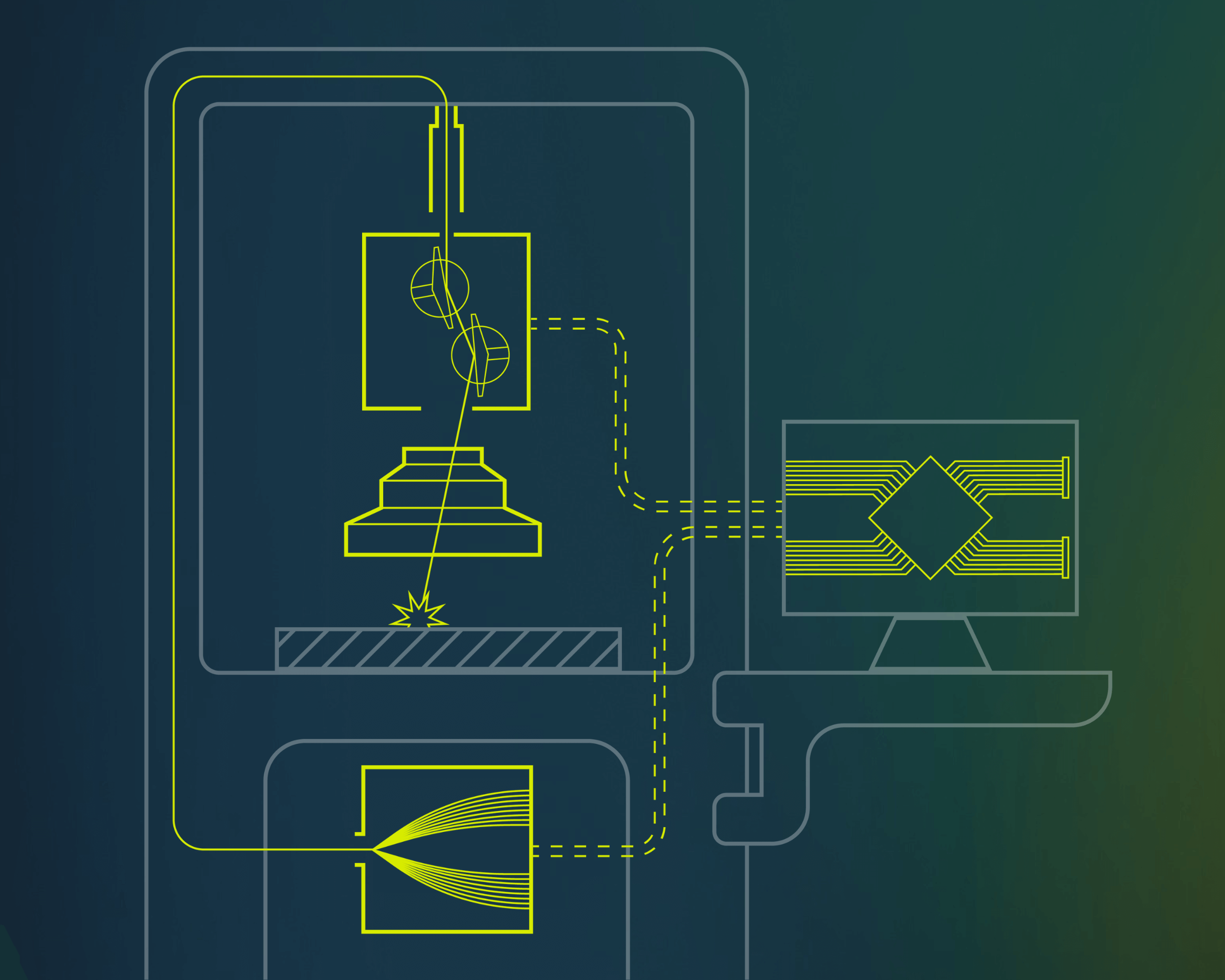
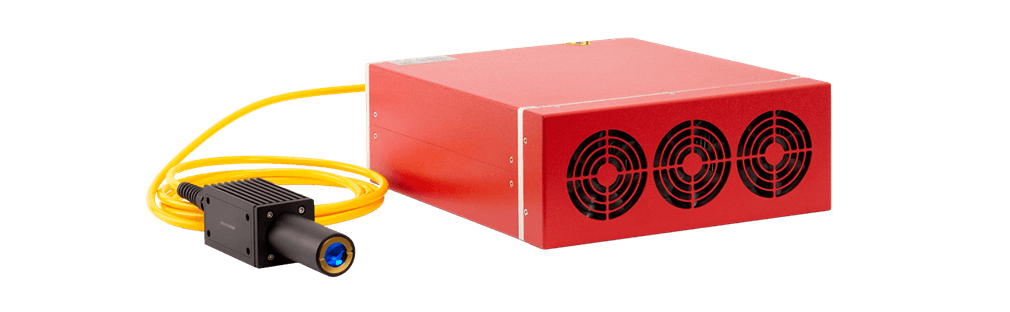
The laser source is the heart of the system.
Depending on the material and marking method, different types of lasers, wavelengths, and laser powers are used. The choice of the laser type and model depends on the specific requirements of the application and the material involved.
Our portfolio includes laser beam sources from 355 to 10600 nm, which are perfectly suited for laser marking. Covering Diode-Pumped Solid-State Lasers (DPSS), pulsed Fiber Lasers, Picosecond Lasers and CO2 Lasers.
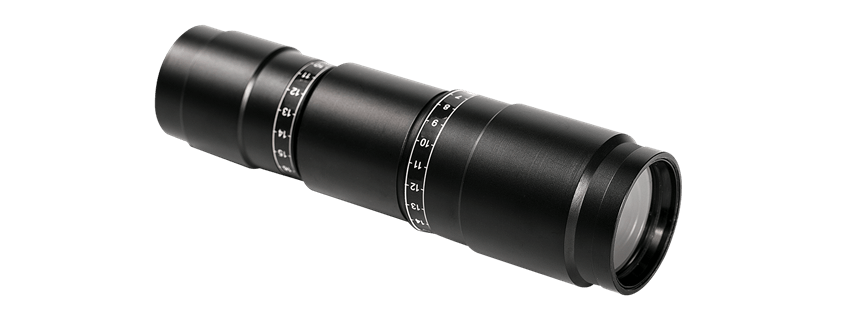
Depending on the output beam diameter of the laser source and the input aperture of the laser scan head, a beam expander can be integrated between both components in certain cases. It allows for fine adjustment of the laser beam diameter, either to increase or decrease, in order to adapt it to the scan head.
The individual adjustment of the beam diameter of the laser source to the scan head and other optical components enables precise and efficient marking by optimizing the focus size and power density on the material.
Beam expanders are available in various sizes for different magnification factors from 1.1x to 20x. In addition to their magnification function, they often allow the beam divergence to be adjusted, depending on the beam expander model chosen.
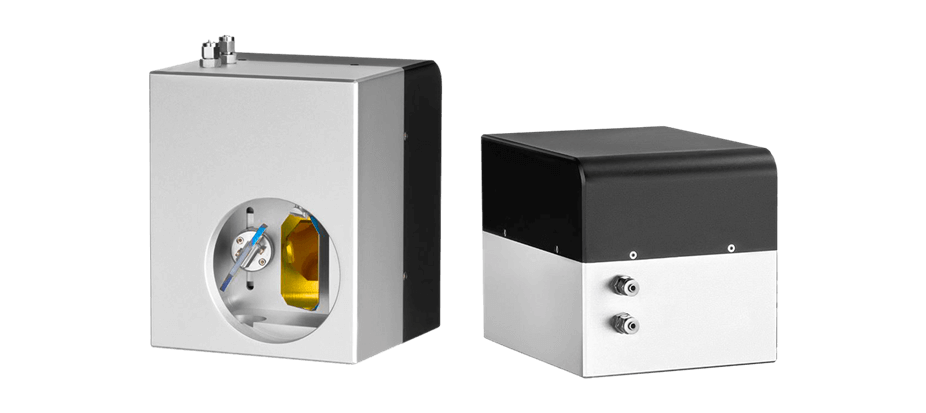
The laser scan head, also known as galvo scanner or laser deflection unit, plays a crucial role in the micron-accurate positioning of the focussed laser beam.
Laser scan heads utilize two movable mirrors that are dynamically aligned in the X- and Y-axes during the marking process, using high-dynamic galvanometer motors. A 2-axis laser scan head can be extended with a pre-focusing 3-axis module to process larger working fields or non-flat materials. As a result, the laser beam can be focused anywhere in an X-Y-Z volume.
By precisely aligning and positioning the laser beam, a laser scan head can transfer complex patterns and fine details onto the workpiece with remarkable speed and accuracy. Fast and precise laser scan heads are crucial for the quality and efficiency of the laser marking process.
The selection of the appropriate laser scan head depends on various factors. These are the most important ones.
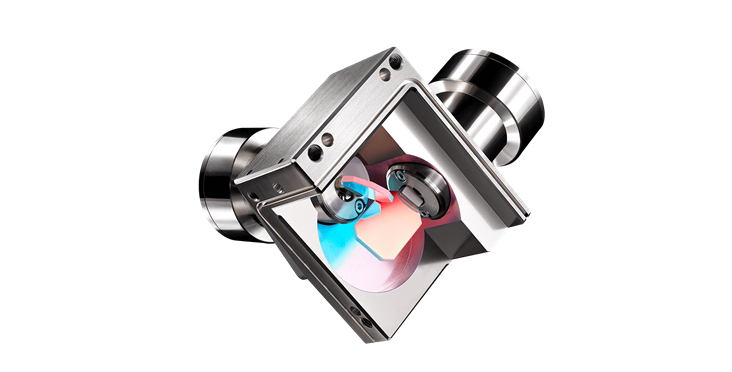
Mechanically mounted galvanometer scanners with X- and Y-mirrors.
F-theta lenses, also known as flat field lenses or plane field lenses, play a decisive role in the design of a laser marking system. Especially in applications with 2-axis laser scan heads or polygon scanners.
They enable extremely precise focusing of the laser beam, with a diameter of just a few µm, on the surface to be marked and are essential for achieving micrometer-precise positioning and high power densities on the workpiece.
Compared to simple single-element focusing lenses, which would image the laser focus onto a spherical shell, F-Theta lenses enable the laser focus to be positioned precisely on a flat working field. The focus size remains constant, which is a decisive advantage for a consistently high quality of laser marking across the entire working field.
Telecentric F-Theta lenses enable especially precise focusing and positioning of laser beams with minimal telecentric error, as the angle of incidence is almost 90° across the entire working field. This characteristic makes telecentric F-Theta lenses particularly suitable for demanding applications in which precise control of the spot symmetry and angle of incidence is required to mark or engrave the material accurately.
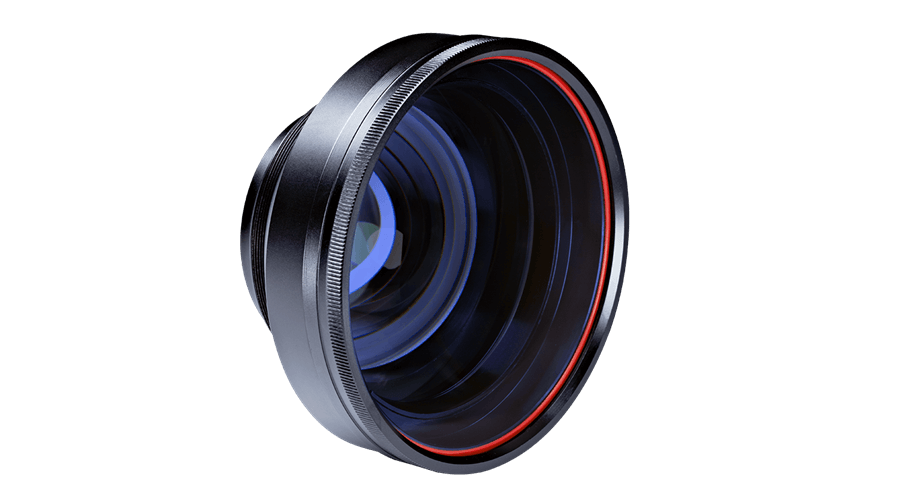
Control cards are used as the interface between the computer that controls the marking tasks and the actual laser marking system including the laser source and scan head.
The control card receives commands from the control software and converts them into precise control signals for the laser source and the laser deflection unit. Modern laser control cards and laser software also enable the high-precision control of additional axes, or process automation.
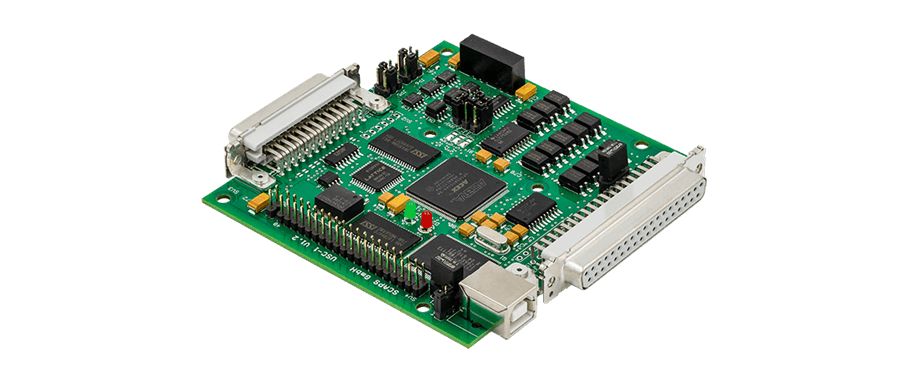
Fume Extraction: Effective extraction is essential for safely removing fumes and particles released during laser marking processes. It ensures not only a clean working environment but also extends the lifetime of optical components and minimizes potential health risks.
Temperature Control: Proper temperature control is essential for maintaining the optimal operating temperature of the laser marking system and all components installed. Both excessively high and excessively low temperatures can affect the laser's or scan head's performance and negatively impact the durability of the system components.
Laser safety: Laser systems are subject to legal requirements for laser safety. They are categorized into different laser safety classes from 1 (safe) to 4 (unsafe) based on their level of protection. Compliance with these requirements is essential to ensure the safety of people working with the laser system. The better the protection class of the system, the more extensive the requirements for the installed safety components.
Typical safety concepts for laser marking systems include various technical measures, such as the integration of laser safety windows, interlocks, emergency stop systems as well as mechanical and electronic shutters.
It is very important that the safety concept is always tailored to the individual system design and the laser installed!
Typical Industries
Laser marking has established itself as an indispensable technology for product marking in numerous industries. Processes are becoming faster, more precise and more efficient.
New trends and areas of application are constantly developing.
Automotive
Laser marking plays a central role in the automotive industry when it comes to marking components with serial numbers, barcodes, logos or design features.
The permanent markings are not only used for traceability, but also for quality management and design. The ability to mark different materials with high precision and outstanding repeatability makes laser marking particularly attractive for the automotive industry.
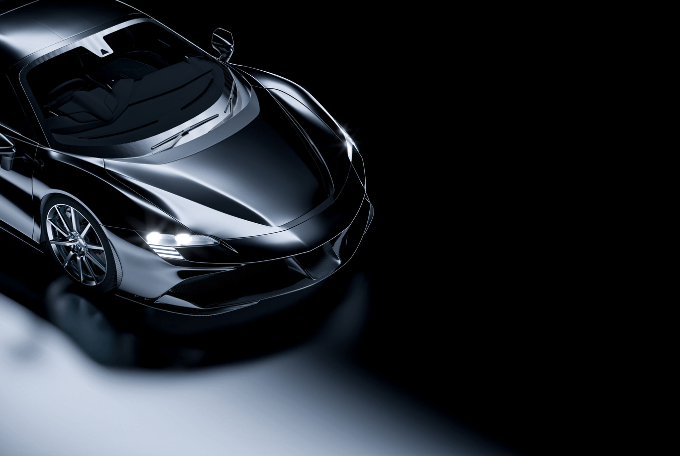
aerospace
A wide variety of components are laser marked in the aerospace industry. Markings serve to ensure traceability and compliance with quality standards.
With well-tuned hardware and process parameters, material-friendly laser marking does not negatively affect the positive properties of the materials used in the aerospace industry. It helps to prevent accelerated wear caused by the marking under demanding conditions.
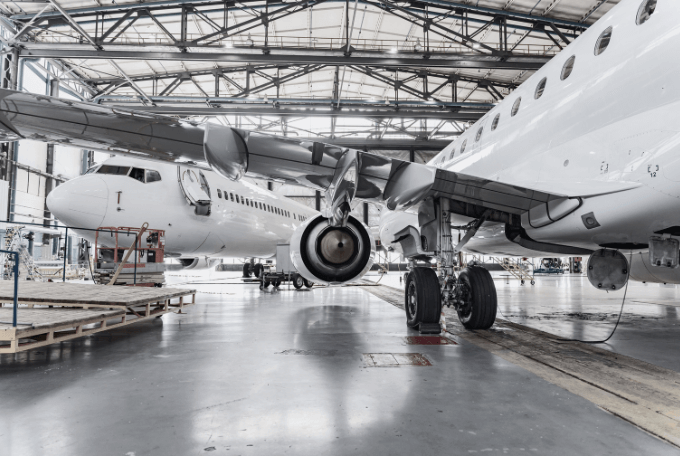
Electronics
In the electronics industry, lasers are used for marking PCB and electronic components. In order to meet the requirements of today's electronics production, precision and speed are of great importance.
Heat-sensitive parts can be laser marked with outstanding precision, even in microscopic dimensions. Non-contact laser marking prevents damage to sensitive components during the marking process and helps to reduce material waste.
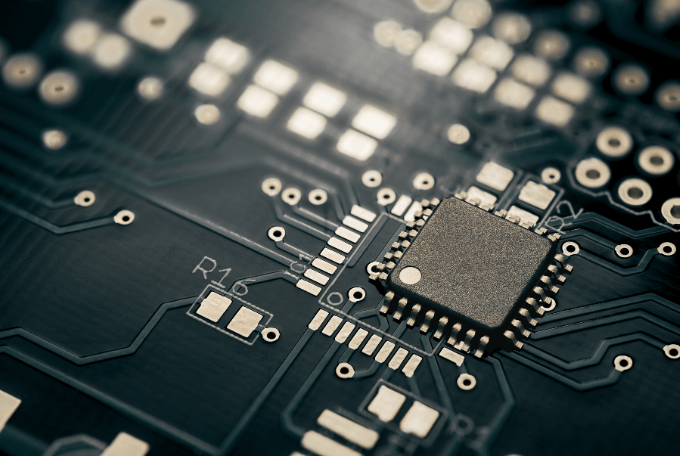
Medical
High-quality marking of medical devices, surgical instruments and implants is essential in medical technology. Laser marking guarantees hygienic and permanent markings meeting the strict regulatory requirements for traceability in the medical sector.
It offers an efficient solution for markings on medical instruments that withstand sterilization processes and demanding environmental conditions.
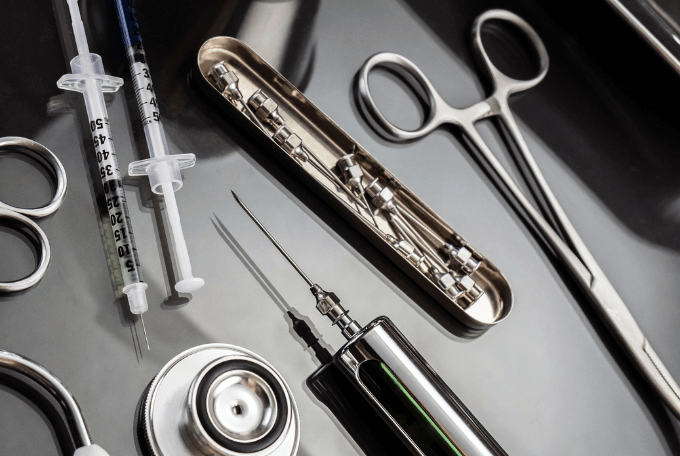
Packaging
Laser marking is used in the packaging industry to mark various packaging materials with product or production information. It meets the requirements for sustainability and process stability at high speed and cost efficiency.
The elimination of chemicals and consumables for packaging marking are two more reasons for its widespread use in the packaging industry today.
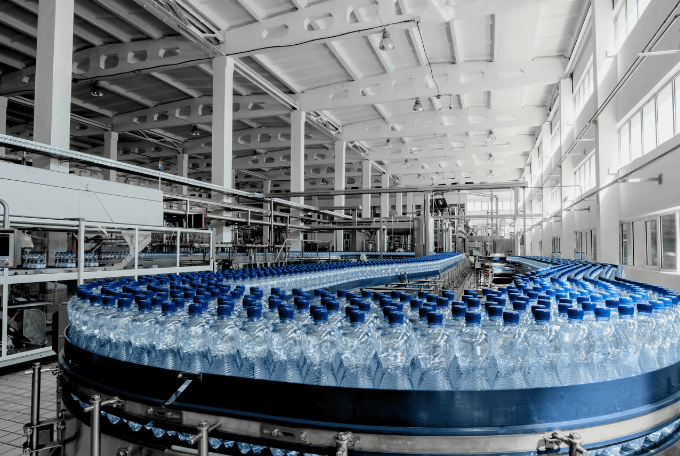
Food industry
Hygienic marking on containers, equipment, and components is essential in the food industry. Laser marking is perfect for this purpose as it generates no contaminants and is easy to clean.
Laser marking allows for the application of information, warning labels, and logos on containers and equipment without negatively affecting the material's positive properties, ensuring hygiene and safety.
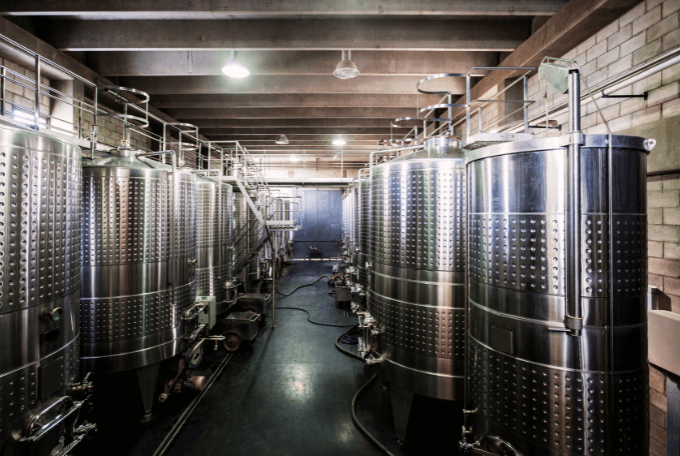